Industrial chillers are essential cooling systems used across various industries, including electroplating, manufacturing, pharmaceuticals, and HVAC systems. These help maintain precise temperature control during industrial processes, ensuring optimal working conditions. By regulating temperature, industrial chillers prevent overheating, enhance product quality, and improve efficiency. In industries like electroplating, where temperature consistency is crucial for quality coatings, chillers play a vital role in maintaining stable conditions. They also offer significant energy savings by optimizing the cooling process. Industrial chillers come in different types, such as water-cooled, air-cooled, and absorption chillers, each suited for specific applications. With their ability to maintain consistent temperatures, these systems help improve operational productivity while reducing the risk of equipment damage. In this article, we will look at the many types of industrial chillers, how they work, and their benefits, specifically in the electroplating and processing industries.
Industrial Chillers for Electroplating Industry
Industrial chillers are designed to lower the temperature of a fluid, usually water, in industrial uses. In the electroplating industry, where metal surfaces are coated with a layer of metal, industrial chillers are used to maintain the temperature of the process and control heat generation during plating. The electroplating process involves the use of electricity to deposit a metal layer onto a workpiece. During this process, excessive heat can be generated, and without proper cooling, the quality of the finish can be compromised.
To ensure high-quality finishes and avoid overheating of components, industrial chillers for electroplating help regulate the temperature of the solution and maintain consistent conditions throughout the plating process.
Specialized Industrial Chillers for Surface Treatment
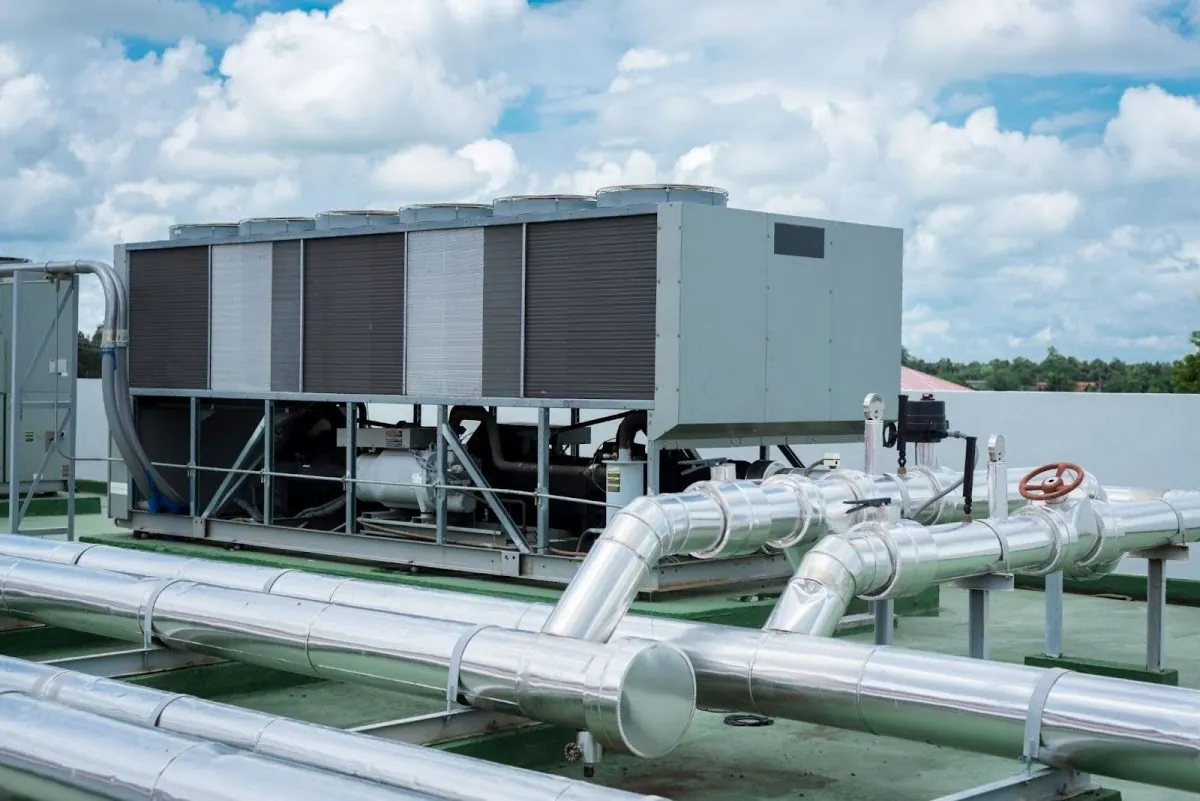
Surface treatment, including processes like electroplating, anodizing, and coating, requires precise temperature control to achieve the desired finish. In these industries, industrial chillers are used to manage the temperature of the chemicals or water baths involved in the treatment process. Overheating can lead to undesirable results, such as poor adhesion, incorrect finish, or even equipment damage. Specialized chillers are designed to provide a steady flow of cold water, ensuring that the temperature remains within a specified range.
For industries like electroplating, where high-quality finishes are critical, industrial chillers for surface treatment offer precise control, ensuring optimal results while improving efficiency and reducing downtime caused by equipment malfunction.
Importance of Industrial Chillers in Various Industries
Industrial chillers are used in many sectors where cooling is essential to maintaining product quality, operational efficiency, and safety. Here’s a brief look at why industrial chillers are so important in various industries:
- Electroplating Industry: As mentioned, in the electroplating process, chillers help maintain consistent temperatures in electroplating baths, ensuring high-quality finishes.
- Manufacturing Industries: In manufacturing, chillers cool down various processes such as injection molding, laser cutting, and welding, which generate a considerable amount of heat.
- Pharmaceutical Industry: The pharmaceutical industry relies on chillers to maintain the temperature of ingredients and products during manufacturing, ensuring safety, stability, and adherence to strict regulations.
- Food and Beverage Industry: Chillers are crucial in the food and beverage industry for processes like cooling liquids, refrigeration, and temperature control in large-scale production environments.
- HVAC Systems: In commercial buildings, chillers maintain comfortable indoor temperatures by cooling air or water used for air conditioning systems.
Types of Industrial Chillers
There are several types of industrial chillers, each suited for different applications based on the cooling needs, environmental conditions, and energy consumption goals.
Water-Cooled Chillers
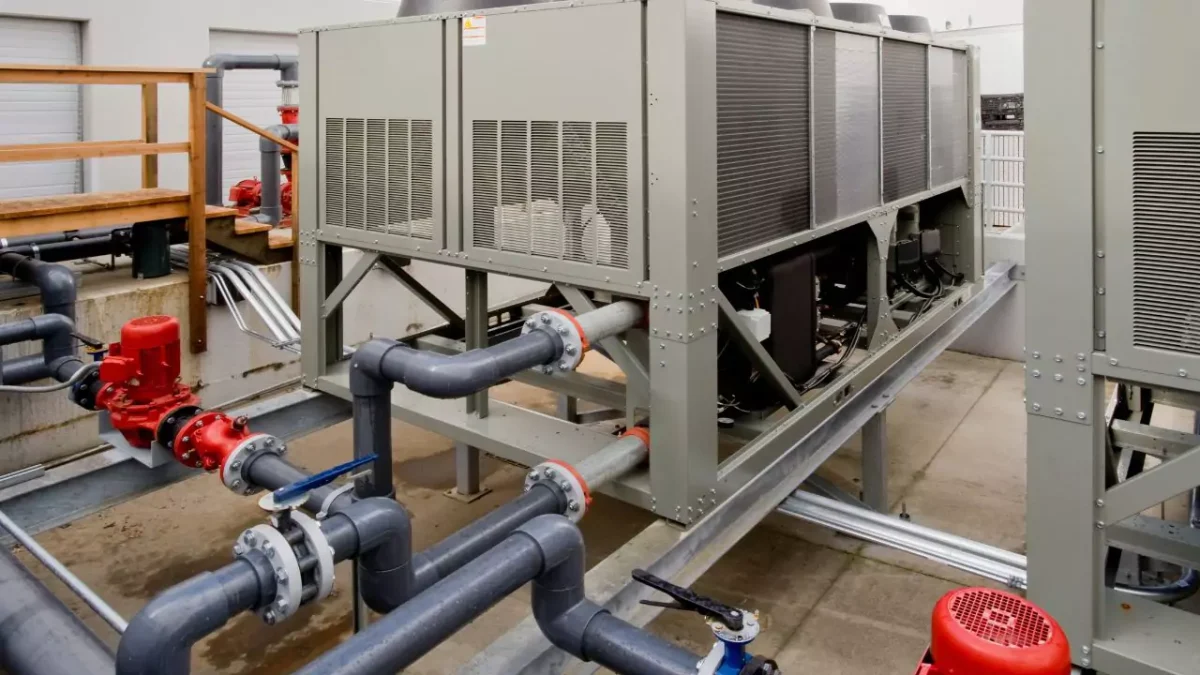
Water-cooled chillers use water to dissipate heat from the cooling process. This type of chiller is usually less noisy than air-cooled chillers because water has a larger thermal capacity and can transport heat better. These chillers require a cooling tower to dissipate heat.
Air-Cooled Chillers
Air-cooled chillers, as the name suggests, use air to cool the refrigerant. The chillers are simple in construction and don’t require a tower for cooling. However, they are typically less energy-efficient than water-cooled chillers and are best suited for smaller applications or where water usage is limited.
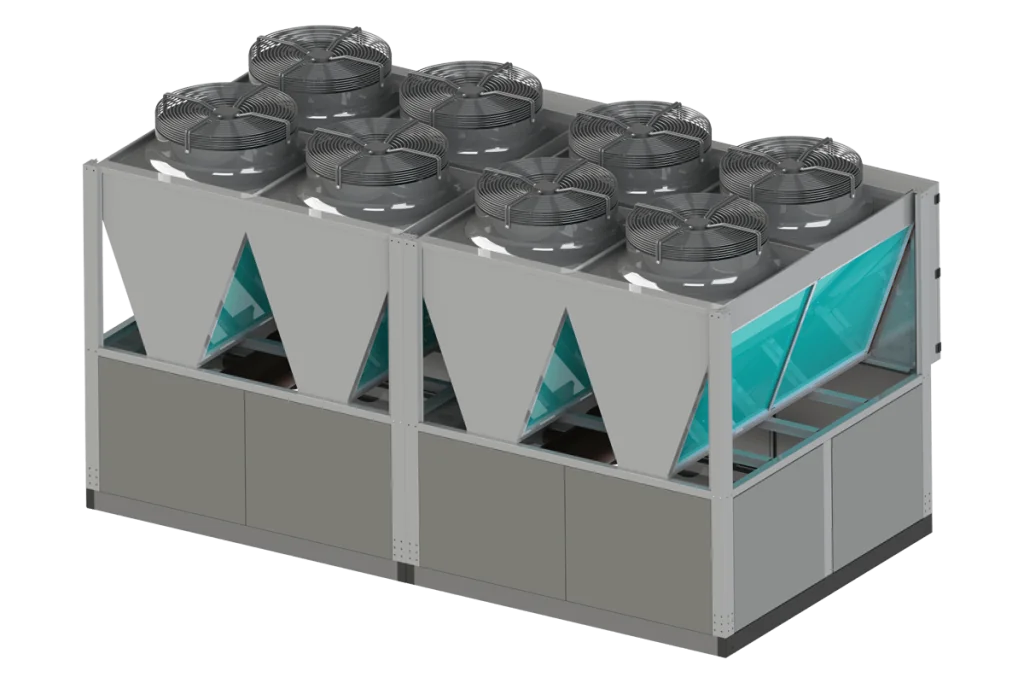
Absorption Chillers
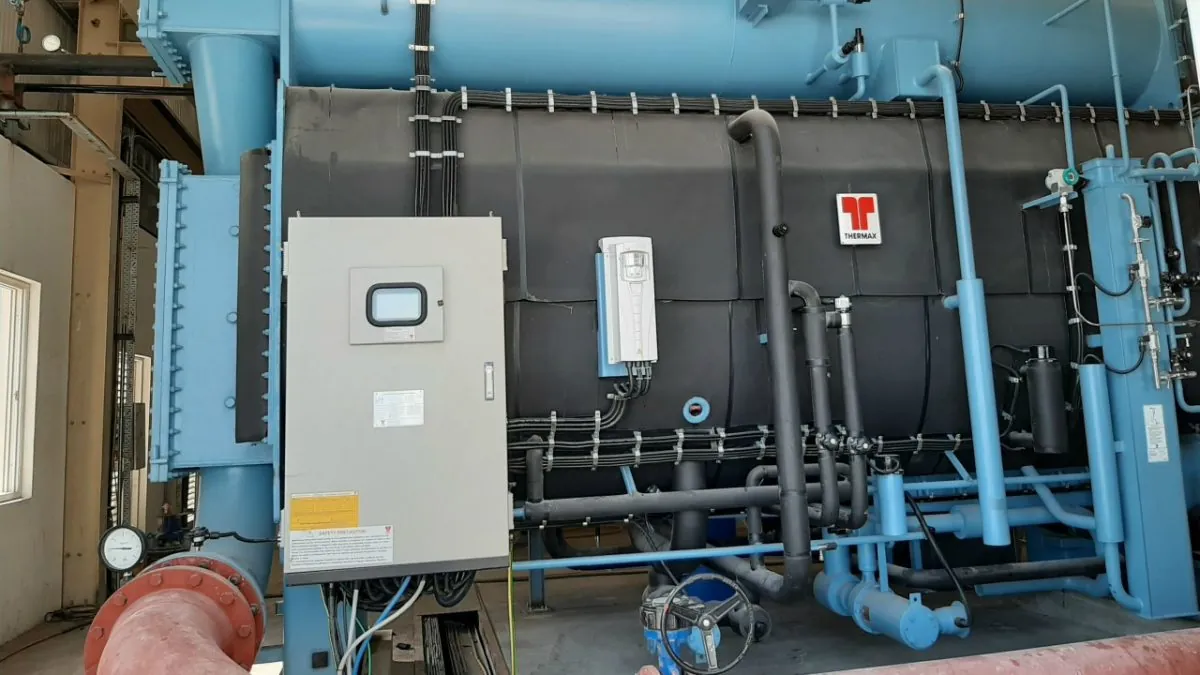
To power the freezing process, absorption chillers utilize heat, often from gas or steam, rather than electricity. These chillers are more environmentally friendly and efficient for large-scale industrial applications where electricity usage is a concern.
Evaporative Coolers
Evaporative coolers use the evaporation of water to reduce air temperature. These are typically used in arid climates where water is more readily available and are often found in HVAC systems for industrial and commercial purposes.
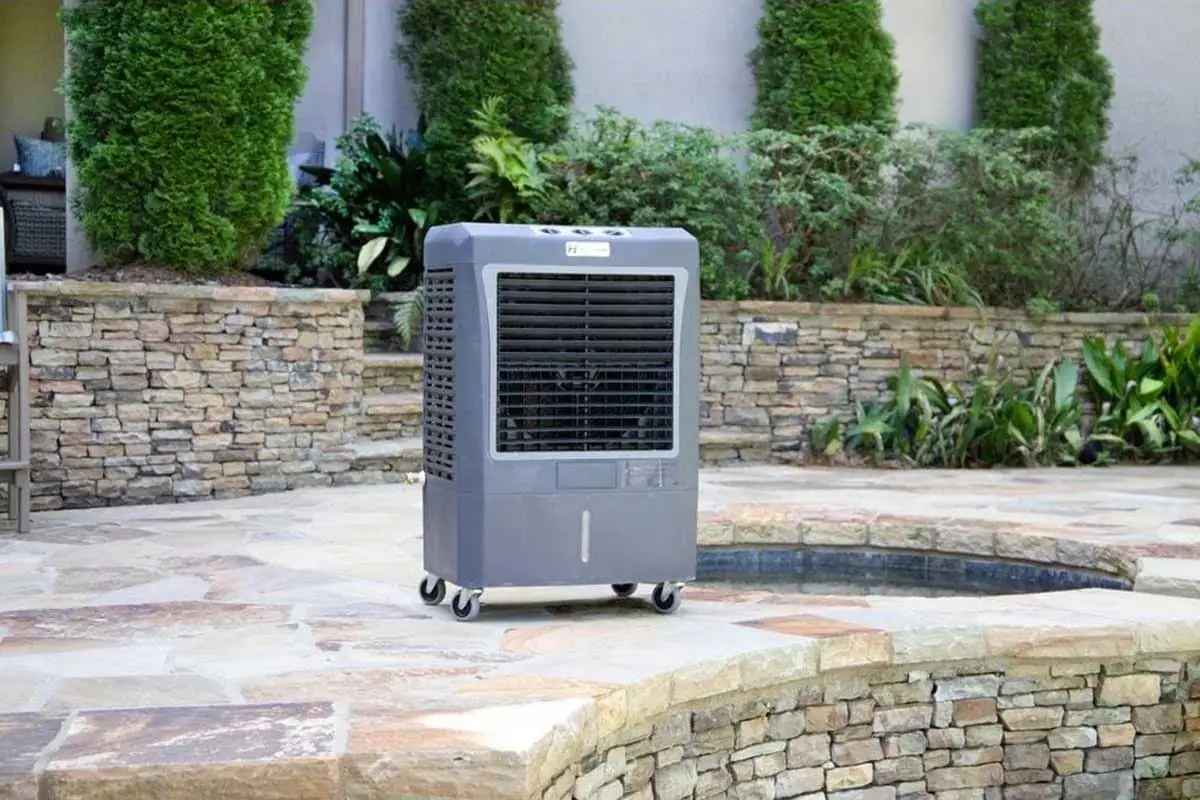
Working Principles of Industrial Chillers
Understanding how industrial chillers work is essential to understanding their applications and benefits. There are three primary cooling cycles used in industrial chillers:
- Compression Refrigeration Cycle : The most common refrigeration cycle in industrial chillers, the compression refrigeration cycle, involves compressing refrigerant gas, which is then cooled and expanded into a liquid. This liquid refrigerant absorbs heat from the process fluid and returns to its gaseous state, repeating the cycle.
- Absorption Refrigeration Cycle : In absorption refrigeration, the cooling process is powered by heat rather than electricity. A refrigerant is absorbed by a substance, typically water, and then evaporated to cool the system. This cycle is often used for large-scale cooling, such as in industrial and commercial settings.
- Evaporative Cooling Process : Evaporative cooling absorbs heat and cools the air or fluid by allowing water to disperse. This process is energy-efficient and typically used in environments where low humidity is present, as it relies on the evaporation of water to reduce temperatures.
Efficiency of Industrial Chillers
The efficiency of an industrial chiller depends on various factors, including the type of chiller, the design, and how well it is maintained. Here’s a look at the key aspects that affect chiller efficiency:
- Energy Efficiency Ratings : Industrial chillers are rated based on their energy efficiency. Higher-efficiency chillers use less power, reducing operational costs and environmental impact. Electricity-efficient chillers are important to businesses looking to cut energy usage and operating expenses.
- Factors Affecting Chiller Efficiency : The efficiency of an industrial chiller can be influenced by factors such as ambient temperature, maintenance practices, the load on the chiller, and the refrigerant used. Proper insulation and efficient heat exchange processes also contribute to better performance.
- Importance of Regular Maintenance for Optimal Efficiency : Regular maintenance is crucial to ensuring that industrial chillers operate efficiently. Maintenance tasks such as cleaning the heat exchangers, checking refrigerant levels, and replacing worn-out parts help prevent inefficiencies, avoid breakdowns, and extend the lifespan of the chiller.
Applications of Industrial Chillers
Industrial chillers are utilized in a variety of industries that demand consistent temperature control. Some common applications include:
- HVAC Systems in Commercial Buildings : Chillers are used in HVAC systems to cool water, which is then used to regulate indoor air temperature. They are commonly found in commercial buildings, shopping malls, and office complexes.
- Cooling Processes in Manufacturing Industries : In industries like injection molding, metal processing, and plastic production, industrial chillers are used to cool machines and materials during the manufacturing process, ensuring optimal performance and quality.
- Medical and Pharmaceutical Industry : Chillers are essential in the pharmaceutical and medical industries for cooling and stabilizing ingredients, products, and laboratory equipment. Temperature control is critical to maintain product quality and ensure safety in these highly regulated industries.
Benefits of Using Industrial Chillers for the Electroplating Industry
The electroplating industry requires precise temperature control to ensure the quality and consistency of metal coatings. Industrial chillers offer several benefits for this industry:
- Energy Cost Savings: By providing efficient cooling, industrial chillers reduce the energy costs associated with electroplating processes. This is especially important in industries with high-volume production, where energy consumption can be a significant portion of operational expenses.
- Environmental Benefits: Modern industrial chillers are designed to be environmentally friendly, using energy-efficient technologies that help reduce emissions and resource consumption. This is vital for industries working toward sustainability and reducing their environmental impact.
- Improved Product Quality and Equipment Reliability: By maintaining consistent temperatures during the electroplating process, industrial chillers improve the overall product quality. They help prevent overheating, which can lead to defects or irregularities in metal finishes. Additionally, chillers reduce wear and tear on equipment, enhancing reliability.
Who is the Manufacturer of Industrial Chillers for Electroplating Industry?
STEP® Techno Solutions LLP is a top industrial chiller manufacturer & exporter, specialized in high-performance chillers for the electroplating industry. With over 25+ years of expertise, it provides reliable and efficient industrial chillers designed to meet the unique cooling needs of the electroplating process. Their chillers ensure optimal temperature control, improving product quality and operational efficiency and reducing the risk of defects. As a trusted industrial chiller manufacturer in India, we offer innovative solutions designed to meet the specific requirements of electroplating industries. Our products are built to withstand demanding environments while delivering consistent, energy-efficient performance. Whether you require cooling solutions for electroplating or other industrial applications, STEP® Techno Solutions LLP offers the best chiller systems to enhance your processes. Contact them today for top-quality industrial chillers to meet your cooling requirements.
Conclusion
Industrial chillers play a crucial role in various industries, ensuring that processes run smoothly by maintaining the correct temperatures. From electroplating to food processing, their applications are vast and critical for achieving consistent results. As the demand for energy-efficient and reliable cooling systems grows, advancements in chiller technology continue to evolve, providing more sustainable and cost-effective solutions.
By understanding the types, working principles, and benefits of industrial chillers, industries can make informed decisions about their cooling needs. Whether you are in the electroplating industry or any other sector requiring precise temperature control, investing in high-quality industrial chillers is essential for efficiency, reliability, and cost-effectiveness.
For more information about industrial chillers for the electroplating industry, STEP® Techno Solutions LLP is here to help. Contact us at +91 98988 75757 or email info@steptsl.com for expert advice and tailored cooling solutions for your business.
FAQ
What is an industrial chiller?
An industrial chiller is a system used to cool liquids or air for industrial processes. It helps maintain the right temperature for equipment, materials, and processes to ensure smooth operations and prevent overheating.
Why do we need an industrial chiller?
Industrial chillers are essential for cooling machinery, products, and processes that generate heat. They ensure efficient operation, prevent equipment damage, and improve product quality by maintaining optimal temperature levels during production.
How does an industrial chiller work?
An industrial chiller works by circulating a coolant through pipes or coils to absorb heat from the environment. The coolant then passes through a compressor, where it’s cooled, and is sent back to continue cooling the system.
What are the different types of industrial chillers?
The main types of industrial chillers are water-cooled, air-cooled, and absorption chillers. Each type has different cooling methods and is suited for specific industries or applications depending on efficiency and environmental conditions.
What industries use industrial chillers?
Industrial chillers are used in various industries, including automotive, pharmaceuticals, food processing, plastics, and HVAC systems. They’re essential for maintaining temperature control during manufacturing, cooling equipment, or processing materials.
How do industrial chillers improve energy efficiency?
Industrial chillers improve energy efficiency by using advanced cooling methods that minimize energy waste. Efficient heat exchange processes, better insulation, and variable speed drives help reduce energy consumption and operating costs over time.
Are industrial chillers customizable for specific needs?
Yes, industrial chillers can be customized based on the cooling requirements of a particular process. Factors like cooling capacity, temperature range, and energy efficiency can be tailored to meet specific industrial applications.
What maintenance is required for industrial chillers?
Routine maintenance for industrial chillers includes checking coolant levels, inspecting components for wear or leaks, cleaning heat exchangers, and ensuring proper operation of compressors. Regular checks keep the chiller running efficiently and extend its lifespan.
How long does an industrial chiller last?
with regular maintenance, an industrial chiller may last 10 to 20 years. Regular service, cleaning, and timely replacement of parts like compressors can prolong the chiller’s life and ensure consistent performance.
Can industrial chillers help reduce production costs?
Yes, industrial chillers help reduce production costs by preventing equipment overheating, improving operational efficiency, and ensuring consistent product quality. With energy-efficient models, they also lower energy consumption, reducing overall operating expenses.