What is an Electroplating Tank?
An electroplating tank is a specialized vessel used in the process of depositing a thin layer of metal on the surface of another material using an electric current. This technique, known as electroplating, enhances the durability, corrosion resistance, and visual appeal of various products, making it vital in industries such as automotive, aerospace, electronics, and even food storage. The electroplating tank holds the electrolyte solution and supports the electrical setup required for the process.Most common varieties are barrel plating tanks for small bulk items, rack plating tanks for big or precious parts, and specialty tanks for brush or pulse plating.. Each type is designed to ensure uniform metal deposition and efficient operation. Electroplating tanks are essential for producing high-quality finishes, protecting against rust, and extending the lifespan of metal components. They allow manufacturers to customize coatings for specific functional or decorative needs, making them a cornerstone of modern manufacturing and product design
An electroplating tank is a purpose-built container designed to hold the electrolyte solution and support the electrical circuitry required for the electroplating process. Electroplating involves passing an electric current through a solution containing metal ions, causing these ions to deposit onto the surface of a workpiece (the cathode), which results in a thin, uniform metal coating. The tank must be constructed from materials that resist corrosion and chemical attack, such as polypropylene, PVC, or lined steel, depending on the chemicals used. The electroplating tank is important because it provides an ideal environment for the plating process, which is essential for getting consistent, high-quality finishes in sectors such as automotive, aerospace, electronics, and jewelry.
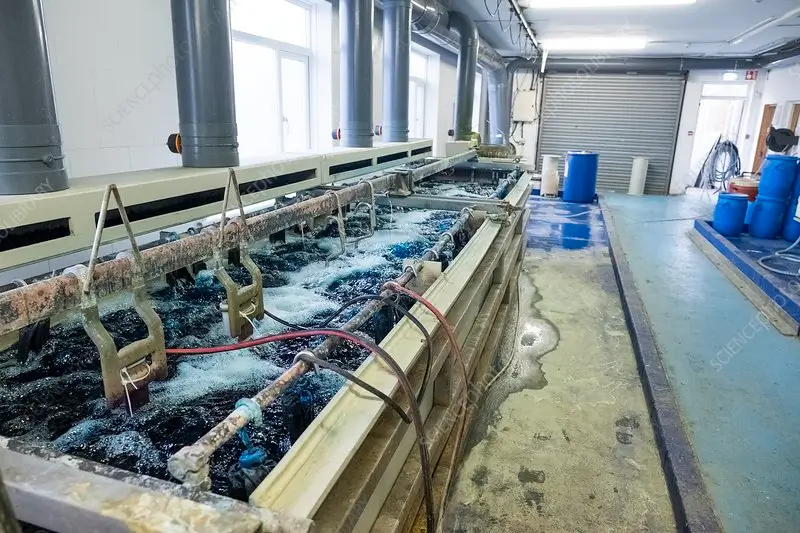
Types of Electroplating Tanks
Electroplating tanks come in several designs, each suited to specific applications and production requirements. The main types include:
1. Barrel Plating Tanks
Barrel plating is ideal for plating large quantities of small, durable parts such as screws, nuts, and washers. In this method, components are placed in a rotating barrel made from chemically resistant material, which is submerged in the electrolyte solution. As the barrel spins, the pieces fall and come into touch with the cathode, making sure equal coverage.
Benefits and Advantages:
- Highly efficient for bulk processing
- Uniform coating on complex shapes
- Cost-effective for small parts
- Reduces manual handling and labor costs
2. Rack Plating Tanks
Rack plating is used for larger or delicate parts that cannot withstand tumbling. Parts are mounted on racks, which are then immersed in the electroplating tank. This setup allows precise control over the placement and orientation of each item, ensuring high-quality finishes for intricate or fragile components.
Techniques Used:
- Custom racks designed for specific parts
- Insulated racks to prevent unwanted plating
- Suitable for large, flat, or fragile items
3. Brush Plating Tanks
Brush plating is a selective process that involves applying metal to specified parts of a workpiece using an electrolyte-soaked brush. While not a tank in the traditional sense, brush plating often uses a small tank to hold the electrolyte and immerse the brush.
Importance and Materials:
- Enables spot repairs and touch-ups
- Minimizes waste and chemical use
- Tanks are typically made from non-reactive plastics
- Useful for maintenance and restoration
4. Pulse Plating Tanks
Pulse plating involves applying electrical current in pulses rather than a steady flow. This technique, used in specialized pulse plating tanks, results in finer grain structures, improved adhesion, and better control over deposit thickness.
Importance and Materials:
- Enhances coating quality and uniformity
- Reduces internal stresses and defects
- Tanks are constructed from materials that withstand rapid current changes and high chemical activity
Uses of Electroplating Tanks
Electroplating tanks are essential in a wide range of industries, each relying on the process to improve product quality and performance.
- Automotive: Electroplating tanks are used to coat engine parts, fasteners, and decorative trims, improving corrosion resistance and appearance.
- Aerospace: Aircraft components require electroplating for enhanced durability, conductivity, and protection against harsh environments.
- Electronics: Circuit boards, connectors, and microchips are plated for better conductivity and wear resistance.
- Jewelry and Consumer Goods: Electroplating tanks provide a lustrous finish and protect against tarnishing.
- Industrial Machinery: Components are plated to extend service life and reduce maintenance.
The importance of the electroplating tank in India has grown with the country’s expanding manufacturing sector, supporting both domestic and export industries.
Benefits and Advantages of Electroplating Tanks
Electroplating tanks offer a multitude of benefits that make them indispensable in modern manufacturing:
- Efficiency: Electroplating tanks enable high-throughput processing, reducing production time and labor costs.
- Cost-Effectiveness: Bulk plating and automation options lower overall expenses while maintaining quality.
- Versatility: Suitable for a wide range of metals and alloys, including copper, nickel, gold, silver, and zinc.
- Environmental Benefits: Well-designed tanks minimize chemical waste and allow for recycling of plating solutions, reducing environmental impact.
- Enhanced Product Quality: Uniform coatings improve durability, corrosion resistance, and appearance, leading to longer product life and reduced maintenance.
- Customization: Electroplating tanks can be tailored to specific processes, part sizes, and production volumes.
Factors to Consider When Choosing an Electroplating Tank
Selecting the right electroplating tank manufacturer involves evaluating several key factors:
- Quality of Materials: Ensure the manufacturer uses high-grade, corrosion-resistant materials suitable for your specific plating solutions.
- Customization: Look for manufacturers who offer custom designs to fit your unique process requirements.
- Technical Expertise: Choose a partner with deep industry knowledge and experience in tank design and installation.
- Cost and Value: Balance initial investment with long-term durability and maintenance costs.
- Customer Service: Reliable support for installation, troubleshooting, and maintenance is essential for smooth operations.
- Compliance: Ensure the manufacturer adheres to environmental and safety regulations.
Who is the Best Electroplating Tank Manufacturer in India?
Selecting the best electroplating tank manufacturer is essential for businesses that demand reliability, safety, and consistent quality in their surface treatment processes. The right partner ensures that every electroplating tank is built with advanced engineering, premium materials, and strict quality control, meeting the diverse needs of modern industry. In India, where the manufacturing sector is rapidly advancing, companies require tanks that offer chemical resistance, durability, and ease of maintenance. With the various electroplating tank manufacturers in India, STEP® Techno Solutions LLP is a popular choice. Renowned for their expertise and commitment to excellence, they provide a comprehensive range of electroplating tanks in India designed for various applications, from automotive to electronics. Their tanks are designed for long life, leak-proof performance, and minimal maintenance, ensuring operational efficiency and cost savings.
When choosing an electroplating tank in India, it is important to consider factors such as product quality, customization options, after-sales support, and industry reputation. STEP® Techno Solutions LLP excels in all these areas, making it the preferred manufacturer for businesses seeking reliable electroplating tank solutions in India that enhance productivity and product quality
Why Choose STEP® Techno Solutions LLP?
For businesses seeking a reliable electroplating tank manufacturer in India, STEP® Techno Solutions LLP stands out for its commitment to quality, innovation, and customer satisfaction. With years of experience as one of the top electroplating tank manufacturers in India, STEP® Techno Solutions LLP delivers tanks that are robust, easy to maintain, and optimized for a wide range of electroplating applications. Their expert team provides end-to-end support, from design and installation to after-sales service, ensuring your operations run smoothly and efficiently.
Conclusion
Electroplating tanks are essential for achieving high-quality, durable, and visually appealing metal finishes across industries. From barrel and rack plating to advanced pulse and brush plating techniques, the right electroplating tank ensures efficiency, safety, and superior results. Explore the possibilities of incorporating an advanced electroplating tank in India into your business and experience the benefits of working with industry leaders. For a solution that meets your needs, reach out to the experts and take your manufacturing capabilities to the next level.tep.
For more details about the electroplating tank, please contact +91 98988 75757 or info@steptsl.com.
FAQ of Electroplating Tanks
1. What materials are electroplating tanks made from?
Electroplating tanks are typically constructed from materials like polypropylene, PVC, or steel lined with resistant materials to withstand corrosive chemicals used in plating baths.
2. What are the main types of electroplating tanks?
The main types include barrel plating tanks for small parts, rack plating tanks for larger or delicate items, and specialized tanks for processes like brush or pulse plating.
3. How does a barrel plating tank work?
Barrel plating tanks rotate small parts in a barrel submerged in electrolyte, ensuring all surfaces are evenly coated during the electroplating process.
4. What is the function of the rectifier in an electroplating tank setup?
The rectifier converts AC to DC current, providing the necessary direct current for metal ions to deposit onto the workpiece during electroplating.
5. Why is agitation important in electroplating tanks?
Agitation helps keep the electrolyte solution uniform, ensuring even metal deposition and preventing defects on the plated surface.
5. Why is agitation important in electroplating tanks?
Agitation helps keep the electrolyte solution uniform, ensuring even metal deposition and preventing defects on the plated surface.
6. How is safety maintained when operating electroplating tanks?
Safety is ensured by using proper tank materials, following manufacturer instructions, minimizing chemical exposure, and using covers to reduce emissions.
7. What industries commonly use electroplating tanks?
Industries such as automotive, aerospace, electronics, and jewelry rely on electroplating tanks to enhance product durability and appearance.
8. How is plating quality monitored in electroplating tanks?
Quality is monitored by controlling current, temperature, and chemical concentration and regularly inspecting the plated parts for uniformity and thickness.
9. What maintenance is required for electroplating tanks?
Regular maintenance includes inspecting for leaks, cleaning residues, checking electrical connections, and ensuring all components function according to specifications.