Chemical immersion heaters are important for industrial processes, especially in chemical processing. These specialized heaters are designed to heat chemicals and liquids directly through immersion, ensuring effective temperature control. By raising the temperature of liquids, they facilitate processes like chemical reactions, blending, and preparing substances for further manufacturing or treatments. These heaters are widely used across various industries, including wastewater treatment, food processing, oil and gas, and pharmaceuticals. They offer several benefits, including energy efficiency, uniform heating, and easy installation. The ability to heat substances directly reduces energy waste, while consistent temperature distribution ensures process reliability.
Chemical immersion heaters are available in different types, such as electric, flanged, and screw plug immersion heaters, each designed to meet specific industrial needs. While they are effective, proper safety measures are essential for safe operation. Regular maintenance checks, safe chemical handling, and employee training help ensure optimal performance and prevent accidents. Here, we will go deeply into the workings, benefits, and applications of chemical immersion heaters, providing a comprehensive guide to their industrial applications.
What are Chemical Immersion Heaters for Chemical Processing?
Chemical immersion heaters are heating elements specifically designed to be submerged in chemicals, liquids, or other substances for the purpose of heating them. These heaters are highly effective in heating materials to a desired temperature quickly and uniformly. They are crucial in many chemical processing operations where maintaining a precise temperature is necessary for optimal reactions or production efficiency.
Importance of Chemical Immersion Heaters in Various Industries
Chemical immersion heaters play a significant role in several industries by enabling precise temperature control during chemical processes. From wastewater treatment to food processing, these heaters ensure that chemicals are heated effectively and uniformly, promoting safety, efficiency, and consistent results. Their versatility and reliability make them indispensable in industries like pharmaceuticals, food and beverage, and oil and gas.
How Do Chemical Immersion Heaters Work?
Chemical immersion heaters work by quickly consuming a heating component in a chemical or liquid. The heat generated by the element is transferred to the surrounding liquid or chemical, raising its temperature. The basic working principle involves the use of electricity or other energy sources to heat the element, which then transfers this heat to the substance it is immersed in.
Description of the Heating Process
The heating element in chemical immersion heaters typically consists of high-quality materials, such as stainless steel or Incoloy, that can withstand high temperatures and the corrosive effects of chemicals. When an electric current is passed through the heating element, it generates heat due to the resistance of the material. This heat is transferred to the chemical or liquid surrounding the element, causing the substance to increase in temperature.
In many cases, the immersion heater may be fitted with temperature control mechanisms to ensure precise temperature regulation, which is essential for processes that require careful control, such as chemical reactions or mixing operations.
Factors That Affect the Efficiency of Chemical Immersion Heaters
Several factors influence the efficiency of chemical immersion heaters for chemical processing. These include:
- Material of the Heater: The material of the heating element plays a significant role in determining the heater’s durability and efficiency. Materials like stainless steel or Incoloy are often chosen for their resistance to corrosion and ability to withstand high temperatures.
- Size and Power Rating: The size of the immersion heater and its power rating affect how quickly and efficiently it can heat the chemicals. Larger and more powerful heaters can heat larger volumes of chemicals at a faster rate.
- Substance Properties: The specific heat capacity and conductivity of the chemicals being heated also affect the performance of immersion heaters. For example, some chemicals may heat up faster or slower depending on their molecular composition.
- Installation Position: Proper placement of the immersion heater in the chemical tank is crucial for even heating. Heaters should be positioned to ensure that the entire volume of liquid or chemical is heated uniformly.
Types of Chemical Immersion Heaters
There are various types of chemical immersion heaters designed for different industrial applications. The most common types include:
Electric Immersion Heaters
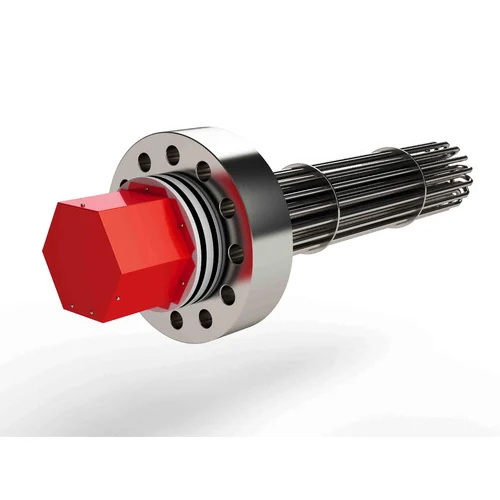
Electric immersion heaters are the most generally used type for processing chemicals. These heaters use electrical energy to generate heat, which is transferred to the chemical or liquid it is immersed. Electric immersion heaters are ideal for precise temperature control and offer efficient performance. They are widely used in a range of applications, from small-scale laboratory processes to large industrial heating systems.
Flanged Immersion Heaters
Flanged immersion heaters have flanged connectors that enable simple attachment to tanks or vessels. These heaters are widely utilized in industries that demand a high amount of heat. The flanged design ensures that the heater is securely mounted and can effectively transfer heat into the liquid or chemical. They are commonly used in larger systems and applications requiring substantial heating capacity.
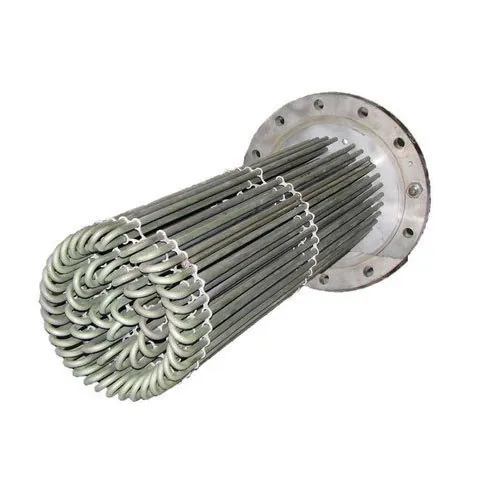
Screw Plug Immersion Heaters
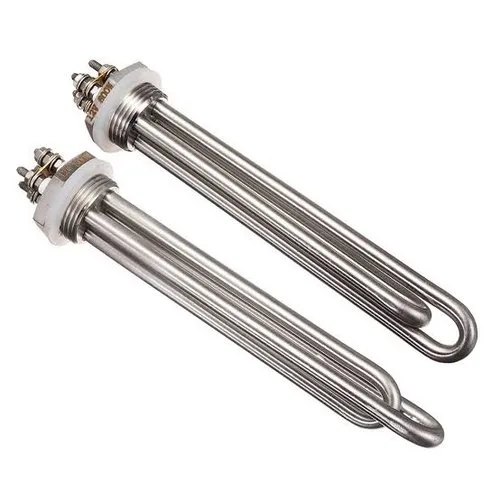
Screw plug immersion heaters are designed for easy installation and maintenance. These heaters are equipped with a screw plug that allows the element to be installed or removed from a tank or container. They are versatile and used in smaller, medium-sized chemical processing operations. The screw plug design also ensures tight sealing to prevent leaks, making them highly efficient for heating liquids and chemicals.
Applications of Chemical Immersion Heaters
Chemical immersion heaters are used extensively in many different industries. Some key applications include:
- Wastewater Treatment Plants : In wastewater treatment plants, chemical immersion heaters are used to maintain the temperature of water, enabling various processes such as coagulation, flocculation, and biological treatment to occur efficiently. Heating the water ensures that chemical reactions happen at the right temperatures for optimal waste removal.
- Oil and Gas Industry : In the oil and gas industry, immersion heaters are used to maintain the temperature of crude oil, natural gas, and other chemicals in pipelines and tanks. Proper heating is essential to reduce the viscosity of oils and ensure smooth flow through pipelines. Chemical immersion heaters are also used in separation processes, such as distillation, where consistent temperatures are crucial for separating different components.
- Food Processing Industry : The food processing industry relies on chemical immersion heaters for various applications, including cooking, pasteurization, and sterilization. These heaters provide precise temperature control, ensuring food products are heated uniformly to the required temperatures, which is essential for both safety and quality.
Benefits of Using Chemical Immersion Heaters
Chemical immersion heaters offer a wide range of benefits that make them a preferred choice for many industries:
- Energy Efficiency : Immersion heaters are highly energy efficient because the heat is directly transferred to the liquid or chemical, minimizing heat loss. This productivity results in decreased energy usage and operating expenses.
- Uniform Heating : One of the key advantages of chemical immersion heaters is their ability to provide uniform heating across the entire tank or vessel. This ensures that the substance is heated evenly, which is critical for consistent quality and efficient processing.
- Easy Installation and Maintenance : Chemical immersion heaters are relatively easy to install and maintain. The design of immersion heaters allows for simple integration into tanks or vessels. Also, heaters with screw plugs are quick to replace or remove for regular consumption, saving time during operation.
Safety Precautions When Using Chemical Immersion Heaters
While chemical immersion heaters are highly effective, proper handling and safety precautions must be followed to avoid accidents and ensure optimal performance:
- Proper Handling of Chemicals : It is essential to follow the manufacturer’s guidelines for handling the chemicals being heated. Some chemicals may be hazardous or reactive to heat, and proper precautions must be taken to ensure the safe operation of immersion heaters.
- Regular Maintenance Checks : To ensure the heater remains in good working condition, regular maintenance checks should be performed. This includes inspecting the heating element for any signs of damage, checking for scale buildup, and ensuring proper insulation and wiring.
- Training for Personnel :Personnel working with chemical immersion heaters should receive appropriate training in their operation, safety protocols, and maintenance procedures. Training ensures that workers can identify potential issues early and follow proper procedures in case of emergencies.
Who is the Manufacturer of Chemical Immersion Heater?
STEP® Techno Solutions LLP is a prominent Chemical Immersion Heater manufacturer and exporter, with over 25+ years of expertise in providing high-quality heating solutions for various industries. Our chemical immersion heaters are designed to offer efficient heating for applications in industries such as wastewater treatment, processing, oil and gas, and pharmaceuticals. As a leading Chemical Immersion Heater manufacturer, we use advanced technology and high-quality materials to ensure reliability and durability. Our heaters are designed to withstand harsh environments and deliver precise temperature control, making them ideal for chemical processing and other demanding applications.
We are completely committed to offering our customers with excellent products that fit their individual requirements. Whether you’re looking for electric immersion heaters, flanged immersion heaters, or screw plug immersion heaters, we offer a variety of options to suit different industrial requirements. As a trusted exporter of chemical immersion heaters, we assure that each product is delivered with excellent service, quality, and performance. Please contact us immediately for information more about our heating options.
Conclusion
Chemical immersion heaters are widely used in a variety of industries, including wastewater treatment, food processing, and oil extraction. Their ability to efficiently heat chemicals and liquids in a controlled manner makes them an indispensable tool in many processes. Understanding how these heaters work, the types available, their benefits, and the safety precautions necessary will help you make informed decisions when choosing the right heating solution for your industry.
For more information about chemical immersion heaters, contact STEP® Techno Solutions LLP at +91 98988 75757 or email us at info@steptsl.com. Let us help you choose the best immersion heaters for your applications and ensure optimal performance in your industrial processes.
FAQ
What is a chemical immersion heater?
A chemical immersion heater is a device used to heat liquids or chemicals by immersing a heating element directly into the substance. It helps raise the temperature for various industrial processes.
How do chemical immersion heaters work?
Chemical immersion heaters work by passing electricity through a heating element, generating heat. This heat is transferred directly to the surrounding liquid or chemical, raising its temperature for various applications like chemical reactions or blending.
What are the types of chemical immersion heaters?
There are different types of chemical immersion heaters, including electric immersion heaters, flanged immersion heaters, and screw plug immersion heaters. Each type is designed for specific industrial applications and installation needs.
What industries use chemical immersion heaters?
Chemical immersion heaters are used in industries like wastewater treatment, food processing, oil and gas, pharmaceuticals, and chemicals. They are essential for controlling temperatures during chemical reactions, blending, and manufacturing processes.
What are the advantages of using chemical immersion heaters?
Chemical immersion heaters offer benefits like energy efficiency, uniform heating, easy installation, and low maintenance. They are ideal for precise temperature control in industrial processes, ensuring consistent quality and reducing energy consumption.
Are chemical immersion heaters energy-efficient?
Yes, chemical immersion heaters are highly energy-efficient. By directly heating the liquid or chemical, they minimize heat loss, making the process more efficient and reducing energy consumption compared to other heating methods.
How do I install a chemical immersion heater?
Chemical immersion heaters are typically installed by inserting them into a tank or vessel containing the liquid or chemical. Depending on the type, some may need a flanged or screw plug connection for secure mounting.
What safety precautions should be taken when using chemical immersion heaters?
To ensure safety, always follow manufacturer guidelines, perform regular maintenance checks, and ensure proper handling of chemicals. It’s also essential to train personnel on proper usage and monitor the heating process to avoid accidents.
Can chemical immersion heaters be used for all types of liquids?
Chemical immersion heaters are versatile and can be used for a variety of liquids and chemicals. However, it’s important to ensure the heater material is compatible with the substance being heated to avoid damage or hazards.
How do I maintain a chemical immersion heater?
Regular maintenance includes inspecting the heater for signs of wear or corrosion, cleaning the heating element to prevent scale buildup, and checking connections for leaks. Proper maintenance keeps optimal performance and increases the heater’s lifetime.